Scalability for comprehensive molding needs
Injection Molding Processes
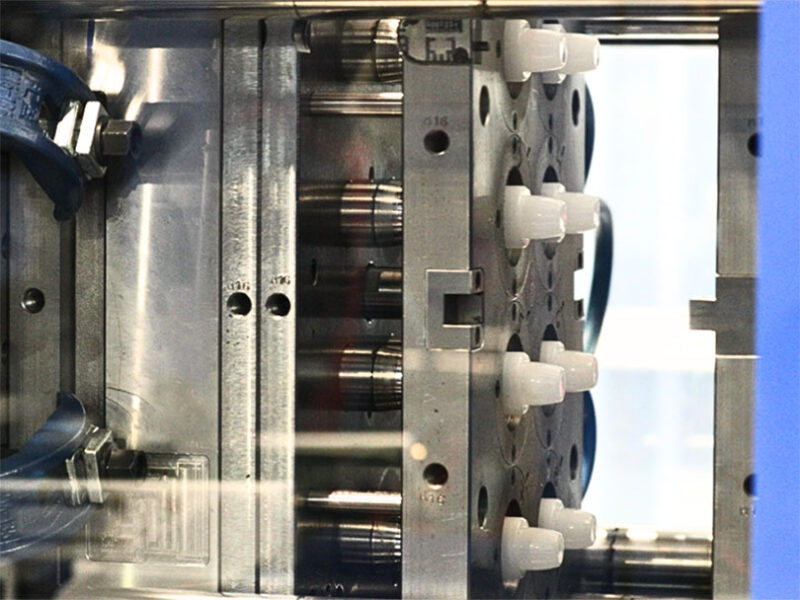
Plastic Injection Molding
Plastic injection molding is a versatile manufacturing process that utilizes high-pressure injection of molten plastic into a mold cavity to produce a wide range of complex and durable plastic products. This is an ideal process for producing large volumes of standardized parts with excellent mechanical properties.
Insert Molding
Insert molding involves the injection of molten thermoplastic around a pre-placed insert to create strong, durable parts. This technique offers advantages like reduced assembly time, improved product reliability and the ability to combine multiple materials in a single part.
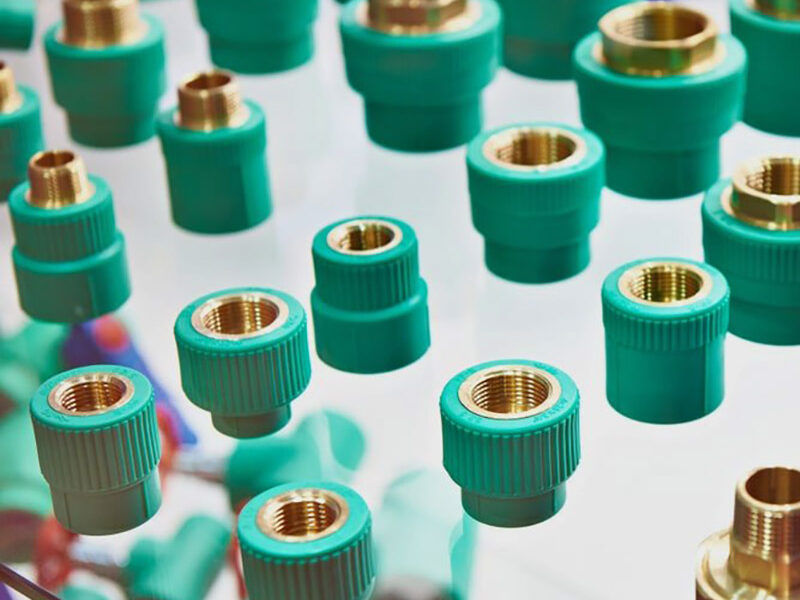
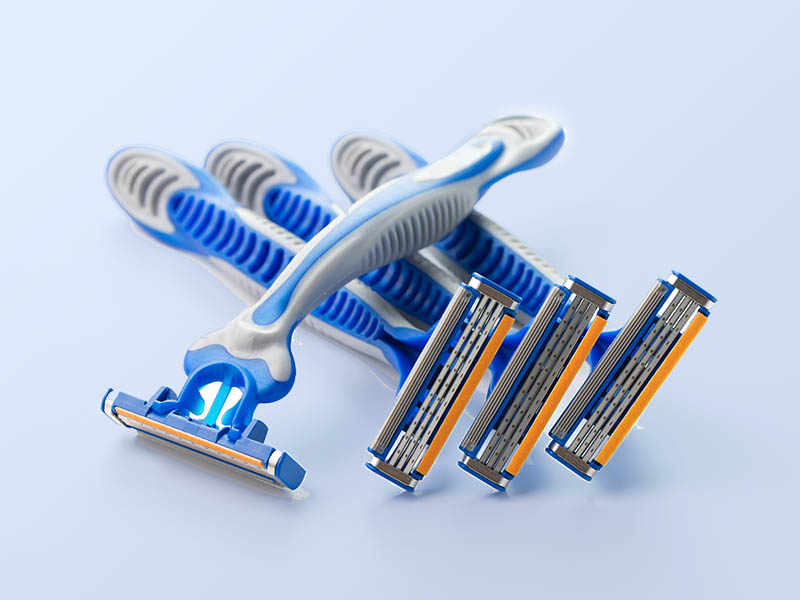
Overmolding
Overmolding is a process in which multiple shots of thermoplastic are injected over or around a substrate to create highly customizable parts. This technique offers versatility and customization options, allowing for the creation of complex and multi-material products with enhanced performance and visual appeal.
Micro Molding
Micro molding is a specialized variation of the injection molding process used to produce small parts with complex geometries. This process allows for the creation of extremely small shot weights, making it a popular option for medical devices, electronics and automotive applications. Micro molding can produce components as small as 0.00025 cc with high quality and repeatability and is compatible with a variety of materials such as PEEK, ABS, Pebax and polypropylene.
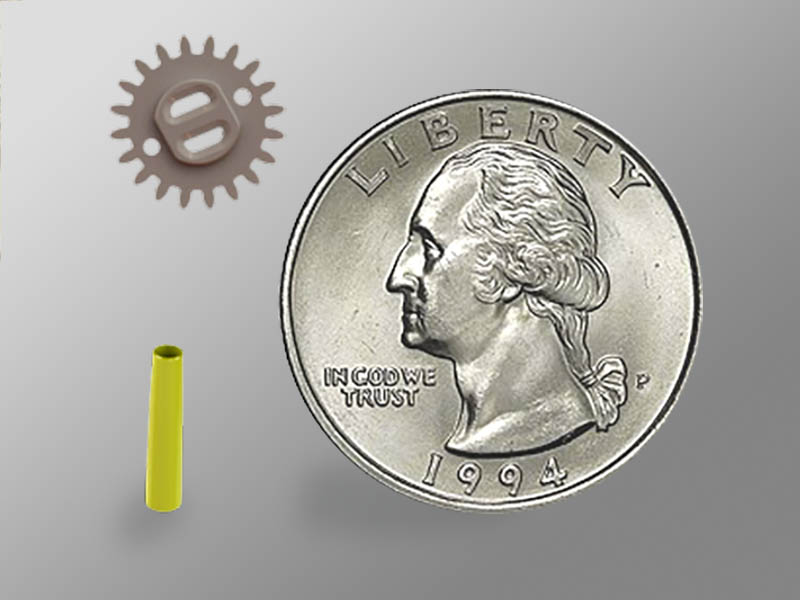
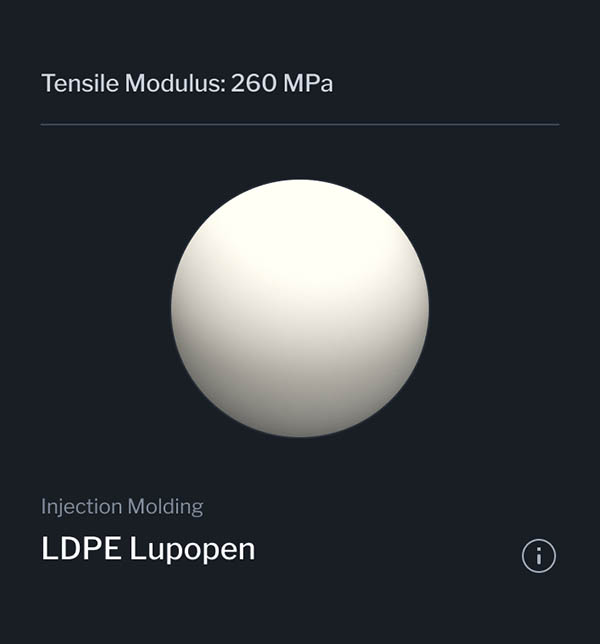
Extensive Material Options and Industry-Best Lead Times
Choose from a wide range of thermoplastics with unique properties to achieve the perfect injection molded parts for your application.
Technology | Type | Materials | Lead Time | |
---|---|---|---|---|
3D PRINTING | Digital Light Synthesis (DLS) | Rigid: CE 221, EPX 82, EPX 86 FR (Flame Retardant), FPU 50, IND 405, MPU 100 (biocompatible), RPU 70, RPU 130, UMA 90 Non-Rigid: EPU 40, EPU 41, IND 147 - HDT 230, SIL 30 | Typically four business days; expedited orders in as few as two business days | |
3D PRINTING | Multi Jet Fusion (MJF) | Standard: Nylon PA-11, Nylon PA-12, PA-12 GF, PP, and TPA Color: CB Nylon PA 12 | Four to five business days depending on material and color | |
3D PRINTING | Fused Deposition Modeling (FDM) | ABS-ESD7, ABS-M30, ABS-M30i, Antero840CN03, ASA, Nylon PA-6, Nylon PA-12, Nylon PA-12 CF (Carbon-Filled), PC-10, PC-ABS, PEKK (Antero 800NA), PPSF, ST-130, Ultem 1010, Ultem 9085, Ultem 9085 CG | As few as three business days | |
3D PRINTING | Stereolithography (SLA) | Accura 25, Black, Color (multiple), Clear, Durable, Elastic, Flexible 80A, High Temp, Surgical Guide (biocompatible), Rigid 4000, Tough 1500, Tough 2000, White | As few as three business days for prototypes; production or high-volume runs are examined on a case-by-case basis | |
3D PRINTING | Direct Metal Laser Sintering (DMLS) / Selective Laser Melting (SLM) | Aluminum (AlSi10), Inconel 625, Inconel 718, Maraging Steel, Titanium (Ti64) | Custom quotes available on a case-by-case basis; lead times vary | |
CNC MACHINING | Most Common: ABS, PC, PE, PP Other Supported Materials: HDPE, LDPE, Nylon (PA 6, PA 11, PA 12, PA 66), PC/ABS, PEEK, PEI, PET, PMMA/Acrylic, POM (Acetal/Delrin), PS, PSU, PU, TPE, TPU, TPV Additives and Fibers: Colorants, flame retardants, glass fibers, plasticizers, UV absorbers | Plastic: ABS, Acetal (Delrin), Nylon 6, Nylon 30%GF, HDPE, PEEK, PC, PTFE (Teflon), PVC, UHMW Metal: Aluminum (2024, 6061, 6082, 7050, 7075), Stainless Steel (303, 304, 316, 17-4, 420), Other Steel (Mild Steel, Alloy Steel, Tool Steel), Other Metals (Brass, Copper, Titanium) T1 Samples: As little as two weeks Post-T1 Approval: As little as one week for orders of <10,000 parts | Eight to 10 business days for orders of <50 parts | |
URETHANE CASTING | Shore D (65 D C85 D) | Standard: ABS-like (80D), PC-like (84D), PE-like (65D), PP-like (70D) High-Performance: 12 Sec Burn (78D), ABS-High Impact (78D), High Impact FR (UL-94V0) (85D), Hi Temp (84D), Nylon/Delrin-like (84D) FDA: ABS-like (80D), ABS-High Strength (85D), Hi Impact Class VI (85D) Clear: Optical Clear (80D, water-clear), PC-like (84D, haze/pale yellow) | First Article (FA): As few as three days, depending on part geometry Post-FA Approval: As little as two weeks | |
URETHANE CASTING | Shore A (15 A C94 A) | Standard Elastomers: 15A C94A High-Performance Elastomers: 15A C90A Water-Clear Elastomers: 45A, 65A, 70A, 90A Silicone: 15A, 25A, 35A, 38A (medical-grade), 40A, 42A, 50A, 53A, 60A, 75A | First Article (FA): As few as three days, depending on part geometry Post-FA Approval: As little as two weeks |